Just as it had happened ten years earlier in IT systems (Data Processing Centers), by the late 1980s, the need to transition from a centralized to […]
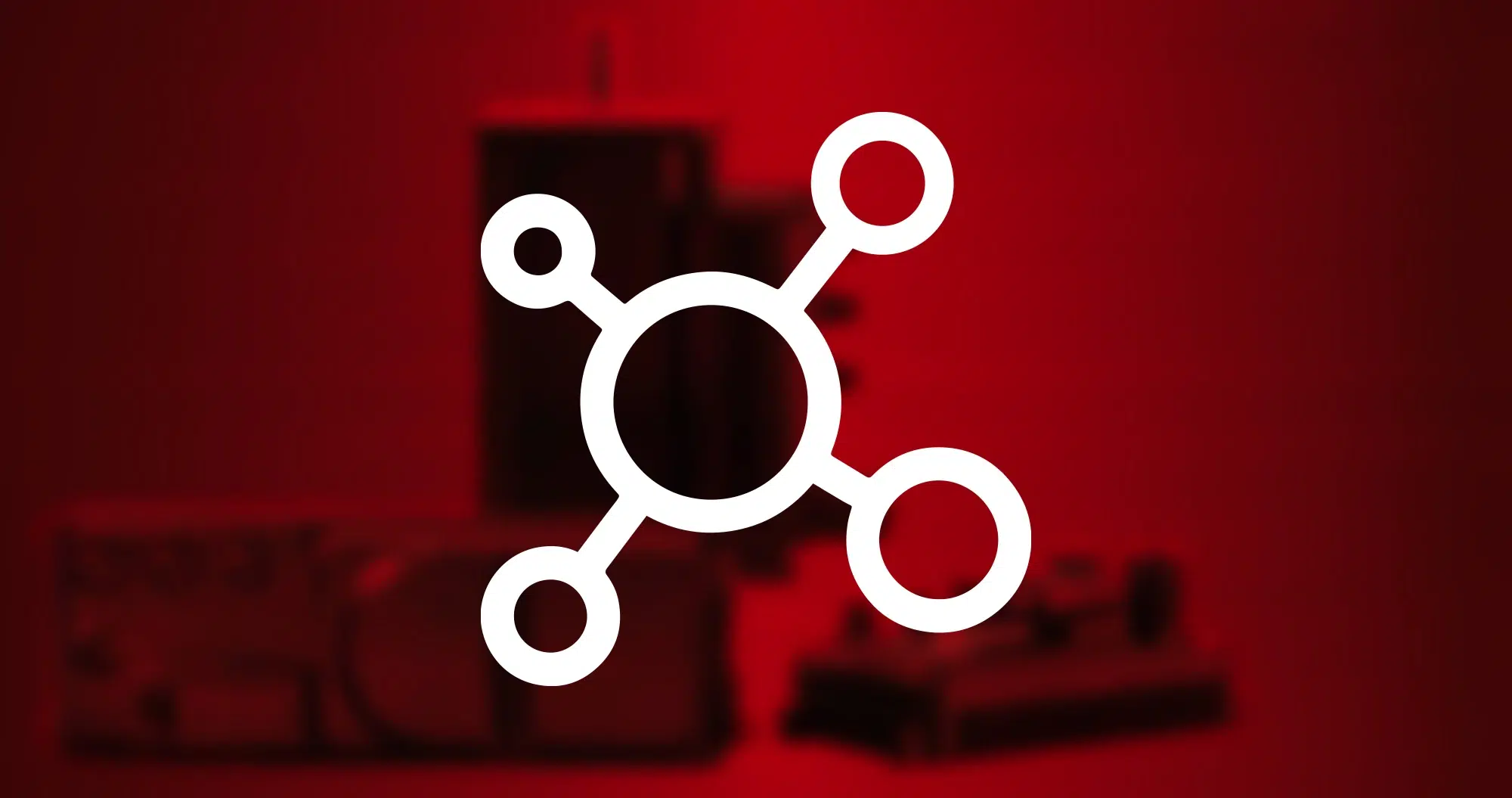
Just as it had happened ten years earlier in IT systems (Data Processing Centers), by the late 1980s, the need to transition from a centralized to a distributed control architecture also emerged in industrial automation systems, particularly in motion control.
New deterministic communication protocols promised synchronized data transmission between “Master” and “Slave” devices. Motion control manufacturers, pioneers of that era, were developing proprietary protocols on various hardware platforms and beginning to connect servo drives using fiber optics. A revolution in motion control was underway!
Those were years of significant change that excited those who were part of them. Witnessing and contributing to this evolution was an honor and a privilege.
The need for standardization quickly became evident, aiming to bring clarity and facilitate control system design. The scope was no longer limited to servo motors alone but needed to encompass sensors and various input/output systems, effectively covering the entire process control chain.
The communication buses that shaped this transformation in control architectures are well known and deserve an entire chapter of their own.
These new “smart” servo drives programmable, flexible, equipped with digital and analog inputs and outputs, and connected via standardized deterministic networks became the building blocks that led to the gradual phasing out of centralized motion control systems and the rise of PC-based motion controllers in distributed architectures
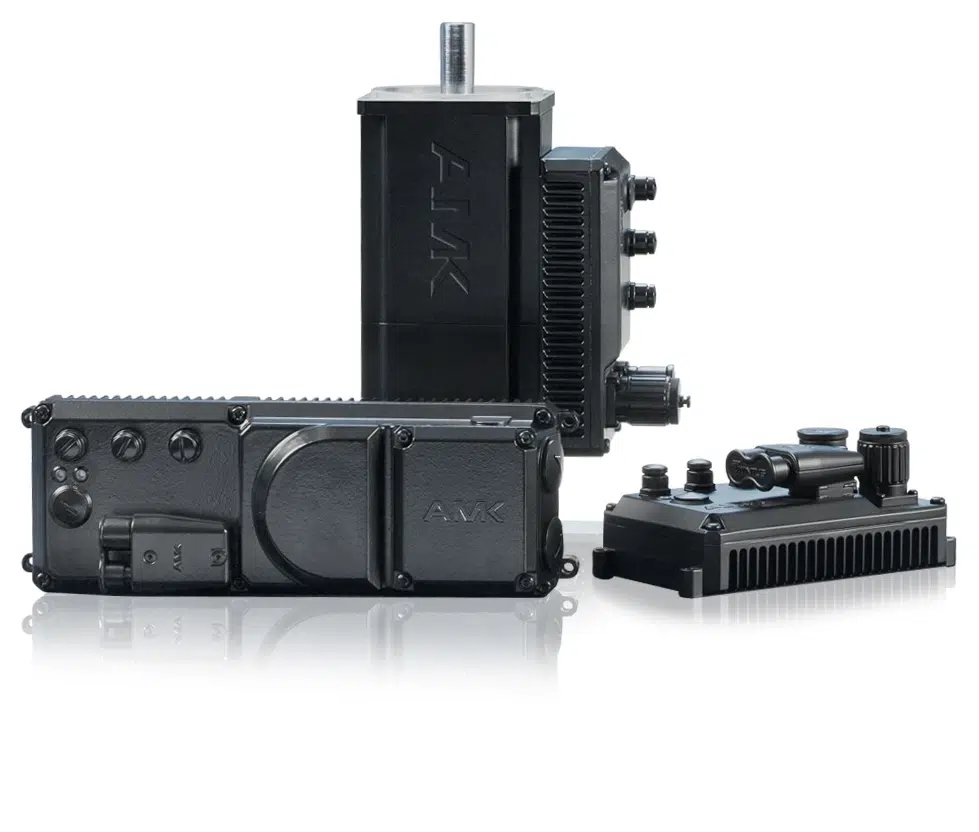
These new control strategies provided a significant boost to machine and process system design, enabling mechanical simplification through the use of even low-power motors, electronically synchronized with local processing capabilities. This not only reduced network traffic but also enabled real-time local functions such as laser source control, position capture within microseconds, execution of electronic camming, and much more.
It was an ideal scenario for designers and innovators who recognized the potential of these new technologies and leveraged them to develop complex yet highly efficient production lines and machinery. These systems could integrate hundreds of intelligently servo-controlled motors of all kinds—rotary or linear brushless, stepper motors, or feedback-equipped solenoids—tailored to the most effective motion solution for each application.
However, this evolution brought and still brings, the challenge of where to install the servo drives, as they are often difficult to accommodate in a control cabinet.
Distributing servo drives across the machine structure or integrating them within the servomotor itself, reorganizing cabling, and managing heat dissipation from power components have become critical issues that must be addressed and resolved.
Here is a brief checklist of fundamental aspects to maximize the benefits of a “physically distributed” onboard machine architecture:
- Choose the correct DC BUS voltage based on the installed power requirements.
- Plan the cabling using standardized and coded cables.
- Consider heat dissipation on the support structure.
- Select the appropriate type of motorization based on performance, size, and protection rating.
- Where possible, adopt a modular approach, both logically and physically.