Generally, when we talk about motion control, we think of high-speed systems with rapid changes in direction. Being able to control motion under these conditions certainly […]
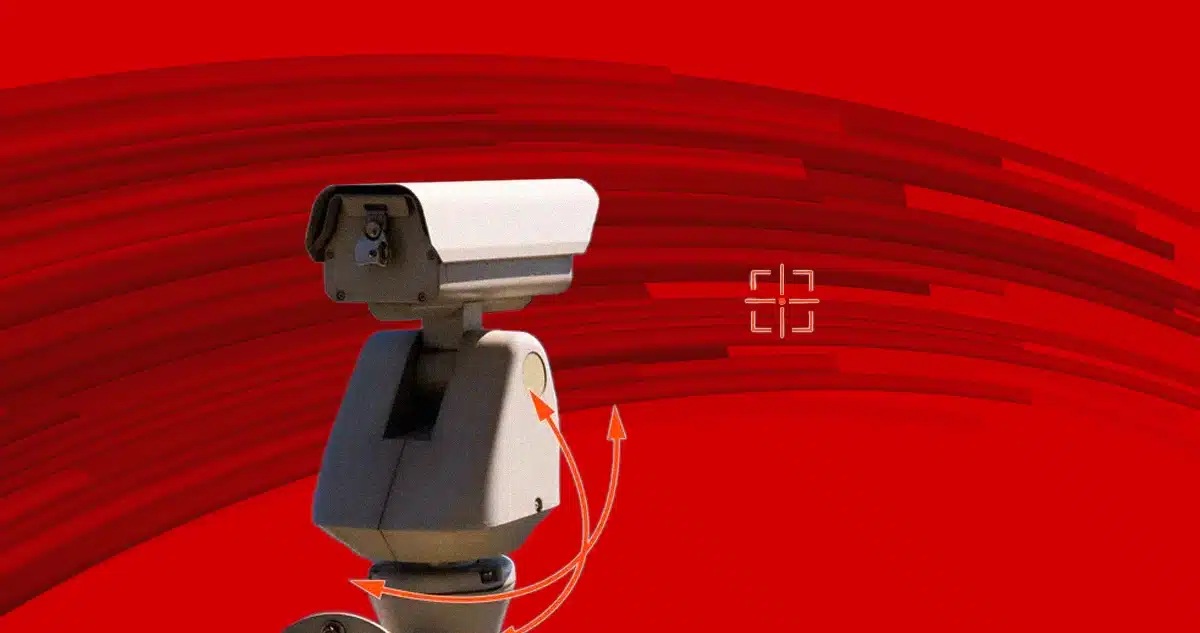
Generally, when we talk about motion control, we think of high-speed systems with rapid changes in direction. Being able to control motion under these conditions certainly presents significant technical challenges; technical challenges arise when you want to control ultra-low speed motion, typically for telescopes or pointing systems, CCTV cameras, and generally in surveillance systems. This session examines the issues arising from an ultra-slow speed system from the perspective of both the position or velocity sensor and the motion controller.
Considering a PTZ (Pan/Tilt/Zoom) pan/tilt/zoom mobile camera, commonly called a “Gimbal System” for video surveillance to borders, it is not uncommon to have to focus on objects as far as 20 km away from the camera. When the object moves, it becomes complex to follow because the field of view is very narrow, and the lens can disappear quickly.
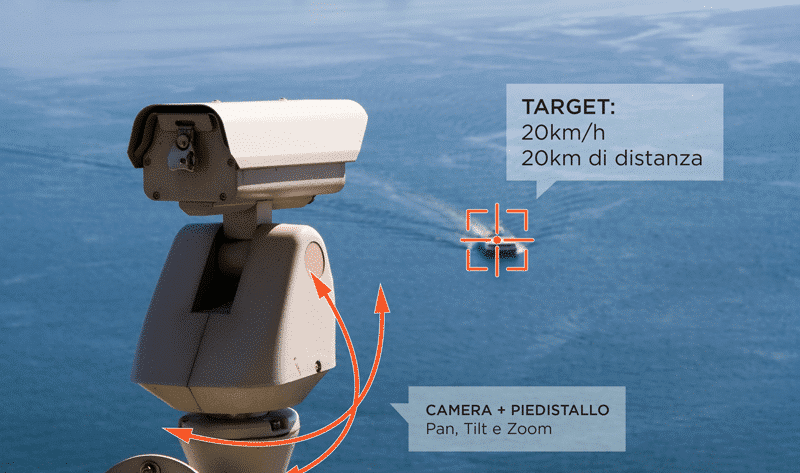
If the target moves at 20 km/hr at a distance of 20 km, the camera will have to rotate at 0.05 RPM, which is a decidedly low speed. To keep the target within the visible area and centered concerning the area itself, one must carefully control this very low speed and quickly follow its direction changes. It becomes essential to use 18- to 22-bit encoders with resolutions of 4194304 counts/revolution, guaranteeing smooth movements even at very low speeds.
The traditional approach uses an encoder on the motor coupled to a gearbox. The greater the reduction ratio, the greater the resolution of the encoder, as seen by the control, proportionally, the overall system will have fewer dynamics and responsiveness, as well as inevitably insert mechanical backlash. All of this leads to the inability to track moving objects, except those placed at a distance that is not great. The alternative is to use a high-resolution encoder directly on the gearbox output shaft to close the position loop at the same time as the one placed on the motor responsible for the speed loop; the type of control is called dual-loop and ensures that gearbox backlash is eliminated resulting in a highly dynamic system. This approach is employed because of the now-available high-resolution position sensors and the development of high-performance Motion Control.
Traditional high-resolution encoders
Traditionally, when we talk about high-resolution encoders, greater than 18 bits equivalent to 1000000 counts/revolution, we identify solutions with resolvers, optical or capacitive encoders. High-resolution resolvers are notoriously expensive and can present engineering problems due to their space requirements, weight, and tight mechanical mounting tolerances. Optical or capacitive ring encoders are similarly expensive and require precision mechanics to deploy. Unlike resolvers, which are very rugged, optical encoders are very sensitive to vibration and shock by employing glass disks, plus the operating temperature is very limited. Both optical and capacitive versions suffer from reliability problems in the presence of dust or condensation. High-resolution optical sensors, employing etched glass disks, are particularly sensitive to foreign objects.
Next-generation inductive encoders
Traditional techniques for achieving high resolutions have limitations; the demand for innovative solutions is growing. An answer to these demands comes with the new generation of inductive encoders that offer resolutions of up to 4 million counts per revolution (22 bits). Inductive encoders, sometimes referred to by the term “incOders,” have the same mechanical robustness as resolvers, offer high resolutions with no contact parts, can work in dirty environments by being immune to dust or foreign bodies, and, finally, can work in the presence of liquids or condensation; they are the solution for designers for encoders that have to work in harsh environments, without having to deal with enclosing them in watertight enclosures as is necessary if optical or capacitive encoders are used. These new position sensors can easily be used with Galil’s next-generation controllers. Sampling times of less than 100µsec make it possible to optimally control motors rotating at very low speeds. Thanks to the 20 MHz bandwidth, an excellent system can be achieved simultaneously, even at high speeds. Integrating “dual loop” control and special resonant filters facilitates fast and effective commissioning.