Talking nowadays, direct motors, or direct drives, is an established technology in many areas of industrial automation. This type of motorization is also finding increasing use […]
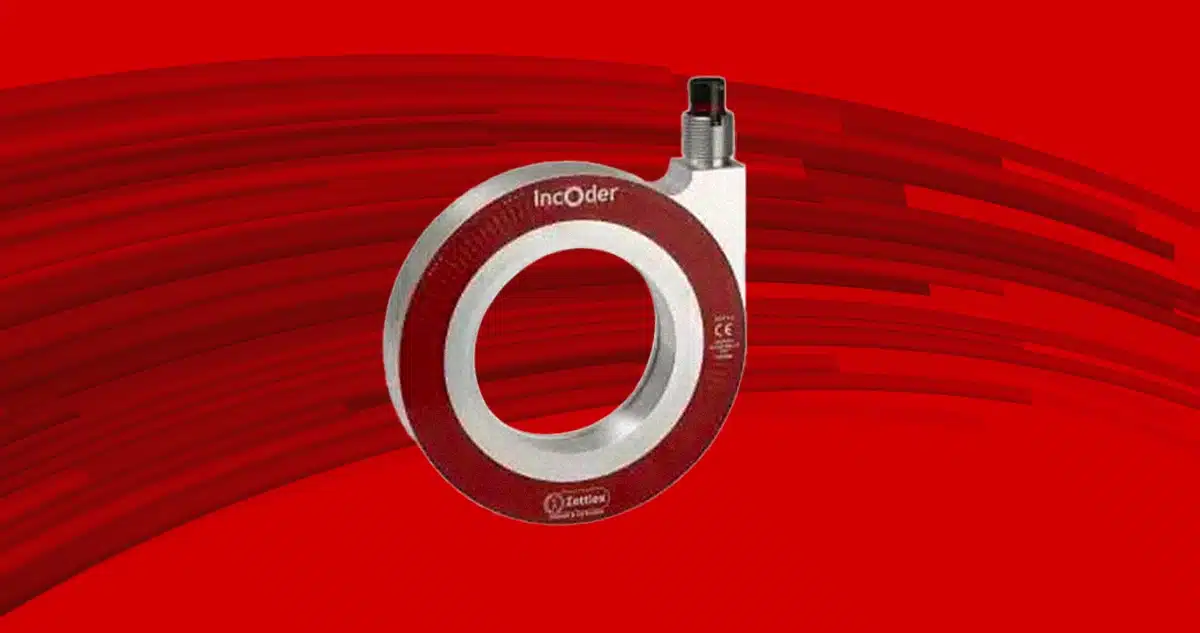
Talking nowadays, direct motors, or direct drives, is an established technology in many areas of industrial automation. This type of motorization is also finding increasing use in fields hitherto reserved for more traditional systems. This article compares possible solutions looking for their advantages and critical points.
Terminology
Theoretically, the term direct motor or direct drive can be applied to any motor to which the load is applied directly without other transmission elements such as gears, pulleys, chains, or gearboxes. It usually refers to using brushless permanent magnet synchronous motors, which directly transmit their torque to the load. They are often developed along the diameter, simultaneously containing the height, and characterized by a through-hole. They are identified as torque motors and develop constant torque at all speeds up to nominal.
How does a direct drive work?
Direct drives work similarly to brushless motors. The magnets are connected to the rotor, while the windings are arranged on the motor’s stator. When the windings are energized, they produce a magnetic field that attracts or repels the rotor magnets causing their controlled rotation. Both rotary and linear direct drives exist.
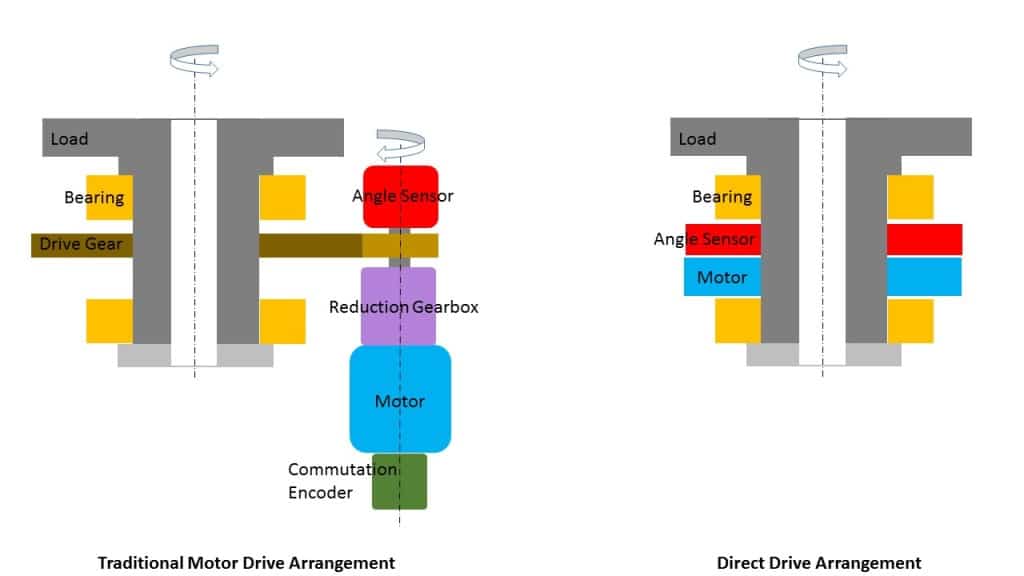
Direct motors usually have many poles (>20 and sometimes > 100); 1 m diameter torque motors are available, capable of producing torques up to 10 KNm. Many are presented as frameless, without housing, bearings, and feedback sensor. This allows machine builders, or integrators, to simplify their housing design and size the shaft and bearings, optimizing their shape, size, weight, and dynamic performance.
The torque-to-inertia ratio is higher than that of conventional brushless motors; they also have a low electrical constant. This means that torque is applied quickly when voltage achieves excellent system stiffness. Traditional motors are designed to generate maximum torque at high speeds, typically over 1000 RPM, and are sized to the rated power. Torque motors, on the other hand, are normally sized on maximum and continuous torque rather than power.
Pros and cons
The major advantages of using direct motors are:
High dynamic performance and accuracy in position and speed control
- Absence of backlash and wear
- High reliability: as there are no mechanical parts such as gears, pulleys, seals, bearings
- Compactness: developing on the diameter, they have a smaller height and have a central hole
- Other torque-to-inertia ratios and another torque-to-mass ratio of the direct motor
- Low ripple (cogging) torque
- High torque at low rpm
- High energy efficiency: due to lack of additional mechanical elements
- Low noise and low self-induced vibration
- Absence of maintenance.
- Low cooling consumption: given the particularly favorable mechanical geometry
- Relatively large air gap: with good impact resistance and excellent solution in dusty environments
The reasons for a designer to choose a direct motor are the possible achievable performance and greater dynamics than traditional solutions. Above all, having a through-hole is a solution to run electrical manifolds, pneumatic tubes, and electrical cables.
The main disadvantage is often more perceived than real; direct drives are sometimes more expensive than conventional motors. This is often true if we compare the cost of the drives. However, a more careful and broader evaluation that considers the mechanical parts that are eliminated, the overall mechanical simplification, and the reduction in maintenance make them, even economically, a winning solution. In addition, the cost of direct motors is gradually decreasing, partly due to the availability of more powerful neodymium iron boron (Nd-Fe-B) magnets and the exponential increase in the use of these drives. A typical example is found in very cost-sensitive applications such as washing machines where conventional motors are being supplanted by torque motors, eliminating belts and pulleys, making motion transmission quieter and more reliable. Major applications of direct drives can be found in CNC machine tools, packaging systems, robotics, radar systems, military, telecommunications, rotary tables, and telescopes. The range is growing, and further expansion is expected in the near future.
Most conventional motors inherently exhibit strong torque cogging, but given the high operating speed, this effect is often insignificant in the final performance. Direct drives may suffer from this drawback more acutely unless feedback with higher resolution is employed. It is certainly one point that has slowed down the use of these new drives by employing more sophisticated controls to command them.
But considerable implementations have also been made in the field of controllers, arriving at sampling times greater than 4 KHz at affordable costs.
One of the major advantages of torque motors is direct transmission and greater accuracy in positioning, speed control, and dynamics. Instead of connecting the load with a coupling, chains or belts, gears or pulleys direct motor flanges to the load; there is no hysteresis, backlash, or lost motion, whatever the direction of positioning. But these advantages are only possible with a high-resolution feedback device. Typically used for power switching, Hall sensors do not offer suitable performance to enable accurate positioning and adequate speed control.
If the direct motor bore is small enough, less than 50 mm, there is a wide range of feedback based on optical, magnetic, or inductive technology. Since most position sensors have a design shape that has a small input shaft, this has led to a problem in integrating torque motors.
The first option is to employ an optical encoder with a DC power supply and absolute or incremental digital output. They are not suitable for dusty or liquid environments, which would compromise proper signal generation. In addition, very tight tolerances, narrow temperature range of use, and strong sensitivity to shock limit their use. Capacitive encoders can overcome these issues, but possible electrostatic discharge is limited. Magnetic encoders have low accuracy due to magnetic hysteresis and are also very sensitive to magnetic fields generated by the motor. The most traditional solution uses resolvers, which give strong reliability and application security, especially in aerospace and defense. However, they are very bulky, heavy, and expensive, especially with holes over 50 mm.
A new approach
A new type of position sensor is increasingly being used as feedback to torque motors, whether inductive or incOders. They use the same electromagnetic or inductive principle as resolvers, but instead of bulky transformer windings, they use laminated printed circuit boards, thus less expensive, more compact, and lighter. Instead of the complex AC power supply and signal processing circuits required by resolvers, incOders use simple electrical interfaces similar to those used by optical encoders, DC power supply, and digital output.
IncOders are available in absolute or incremental formats, A and B signals, with resolutions up to 22 bits, about 4 million counts per revolution. Accuracy less than 40 arc-seconds, or 0.01°, and very low coefficient of thermal expansion, less than 0.5 ppm/K. Dynamic performance has been improved by achieving refresh rates of 10 KHz. Also, constructively they are ideal applications with a large diameter, very low profile, and large through-hole. They can be mechanically attached to the direct motor without additional mechanical parts such as bearings, gaskets, or couplings.
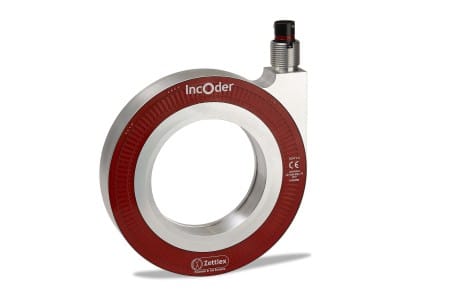
The combination of incOders and torque motors is increasingly preferred by many integrators. The results confirm that they enable highly reliable, dynamic, and precise positioning control even for medical, aerospace, industrial, and petrochemical systems.