Introduction Sliprings play a crucial role in industry, being pivotal components in a wide range of critical applications and high value-added processes. Their primary function is […]
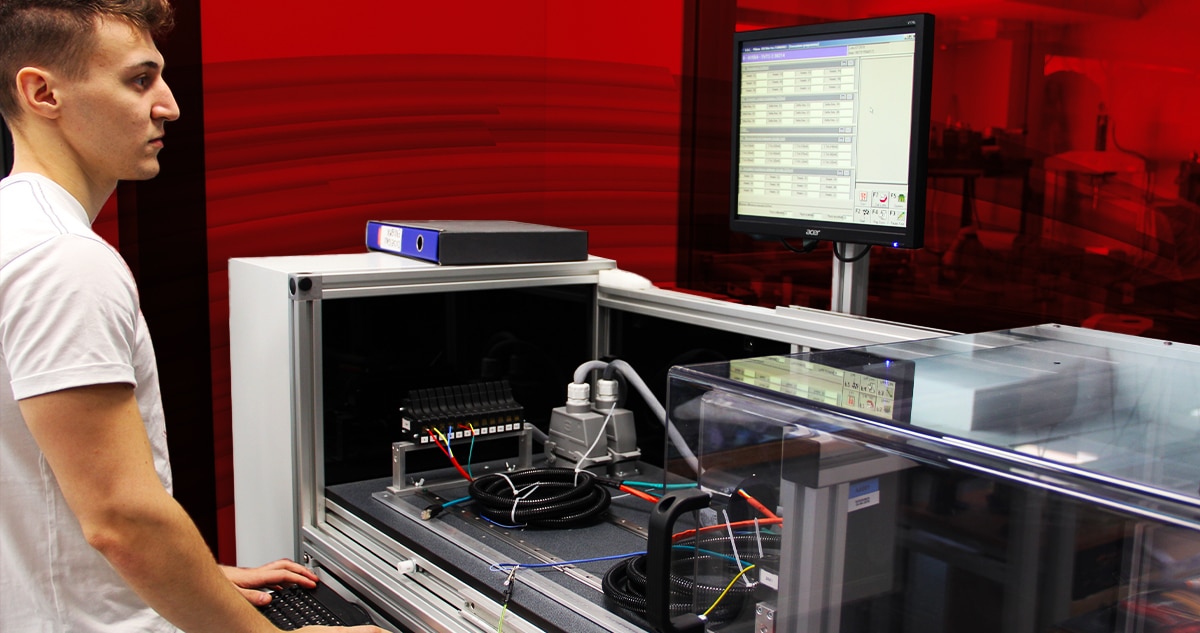
Introduction
Sliprings play a crucial role in industry, being pivotal components in a wide range of critical applications and high value-added processes. Their primary function is to establish a continuous electrical connection between fixed and rotating parts, allowing uninterrupted transmission of signals and electricity. In sectors such as aerospace, wind energy, advanced industrial production, and many others, sliprings are the backbone of complex systems, ensuring that rotation and power transmission occur without interruption. The peculiarity of these devices is that they represent a real bottleneck: all electrical connections for the rotating part pass through the slipring. This functional centrality makes sliprings a Single Point of Failure (SPoF), the failure of which can bring the entire system or process to a standstill. In contexts where downtime entails high costs, the quality and reliability of sliprings become paramount. Strict quality control is therefore essential to ensure the uninterrupted operation of machinery and industrial processes, where every moment of downtime can result in significant losses. This article aims to explore the path sliprings take, from the design phase to the various quality tests, to ensure that they meet the high standards required by modern industrial applications.
The Slipring Design
In an industry where each application can present unique challenges, the ability to provide tailor-made solutions is of paramount importance. Servotecnica excels at this, thanks to a robust design methodology that sees more than one design produced per day, responding precisely and efficiently to specific customer requirements. The design process makes use of document management software (EDMS), which ensures flawless traceability of each design phase, and allows for optimal information management, from initial conception to final product realisation. The ISO 9001 certification, which also covers design, testifies to the commitment and strict adherence to quality standards that characterise each of our projects.
During this crucial phase, we are also able to carefully plan specific quality tests and test equipment based on customer requirements. This advance planning allows us to integrate testing and verification requirements directly into the design, ensuring that the slipring products not only meet, but exceed expectations in terms of performance and reliability.
Our team of highly skilled professionals not only drives innovation through accurate and functional designs, but are also able to guide clients through the process, ensuring that the proposed solutions perfectly meet their needs. This client-centric approach, combined with technical expertise and precise documentation, makes every slipring designed a highly reliable product that is perfectly aligned with customer requirements. Customisation is not just a buzzword, but an established practice that allows us to respond promptly to the most complex challenges, confirming our position as a leader in customised slipring design.
Materials Used
The quality and performance of a slipring is closely linked to the materials used in its construction. Particular attention is paid to the choice of materials for the plating of the rings and brushes, where one opts for a silver alloy or a gold alloy depending on the desired performance. Gold alloy, for example, may offer better conductivity and resistance to oxidation, while silver alloy may be preferable in applications where other electrical characteristics or greater cost containment are required.
Another crucial aspect is the selection of cables and connectors, which must be chosen according to the usage environment considering factors such as chemical compatibility, resistance to vibration and shock, and the degree of protection required. Housing materials, typically ABS plastic or aluminium, are selected to ensure adequate protection and optimum durability. However, we can develop solutions with different steel grades or provide special coatings such as Surtec to meet specific needs. Our expertise in plastic printing and CNC machining processes contributes to the precision and quality of the finished product.
Inspections of the incoming material are another key step to ensure quality. We carry out rigorous checks on the thickness of the plating and its uniformity, as well as tests on the adhesion of the plating to the substrate. In addition, we have the capability to conduct salt spray and temperature tests to evaluate the resistance of materials under extreme conditions. This meticulous attention to material selection and testing is a cornerstone in our commitment to provide high quality slipring that meets and exceeds customer expectations in a wide range of industrial applications.
Manufacturing Process
The slipring manufacturing process is a skilful mix of craftsmanship and standardisation, where manual expertise is combined with well-defined procedures to guarantee a high quality product. The process is largely manual, carried out by qualified personnel who, before working independently, spend at least two years in coaching to assimilate the necessary skills and experience. This intensive training ensures that each member of the team has a thorough understanding of the nuances and precisions required in slipring manufacture.
The production phase follows detailed procedures in line with ISO 9001 certification, thus ensuring standardisation and compliance with international quality standards. These procedures, together with the experience of the staff, ensure the production of products that meet the required technical specifications.
This holistic approach to manufacturing, which values individual skill as much as procedural compliance, enhances our ability to produce customised solutions. The non-fully automated nature of the process gives us greater flexibility, positioning us as a reliable partner for the supply of high-quality slipring, ready to meet customers’ most stringent requirements in terms of performance and reliability.
Quality Testing
Once the manufacturing process is complete, each slipring goes through a rigorous series of quality tests to ensure that it meets all technical specifications and performance requirements. A key role in this phase is played by our customised test machine, called ‘Enigma’, which is designed and manufactured in-house to perform a wide range of both static and dynamic electrical tests. Among the tests performed are resistance measurement, rotational resistance variation, dielectric strength testing both between circuits and to ground, and insulation testing between circuits and to ground.
For sliprings with Ethernet connectivity, an additional static test is performed using a specific certifier, ensuring compliance with regulations and the performance required for network applications. In addition to these standard tests, we also perform dimensional checks to ensure that each unit meets the specified tolerances.
In addition, to meet special needs or specific applications, we can design and build custom test machines. These dedicated tools allow us to conduct special tests and provide customers with confidence that the sliprings supplied are ready to meet the most demanding operational challenges.
A key aspect of our approach to quality testing is ensuring traceability. We are able to store and retrieve test data for each individual slipring, providing customers with the ability to verify product performance and compliance after the fact in case problems emerge on the machine. Together, these testing procedures represent a firm commitment to quality assurance, confirming Servotecnica’s ability to provide reliable, high-quality products ready for deployment in critical operating environments.
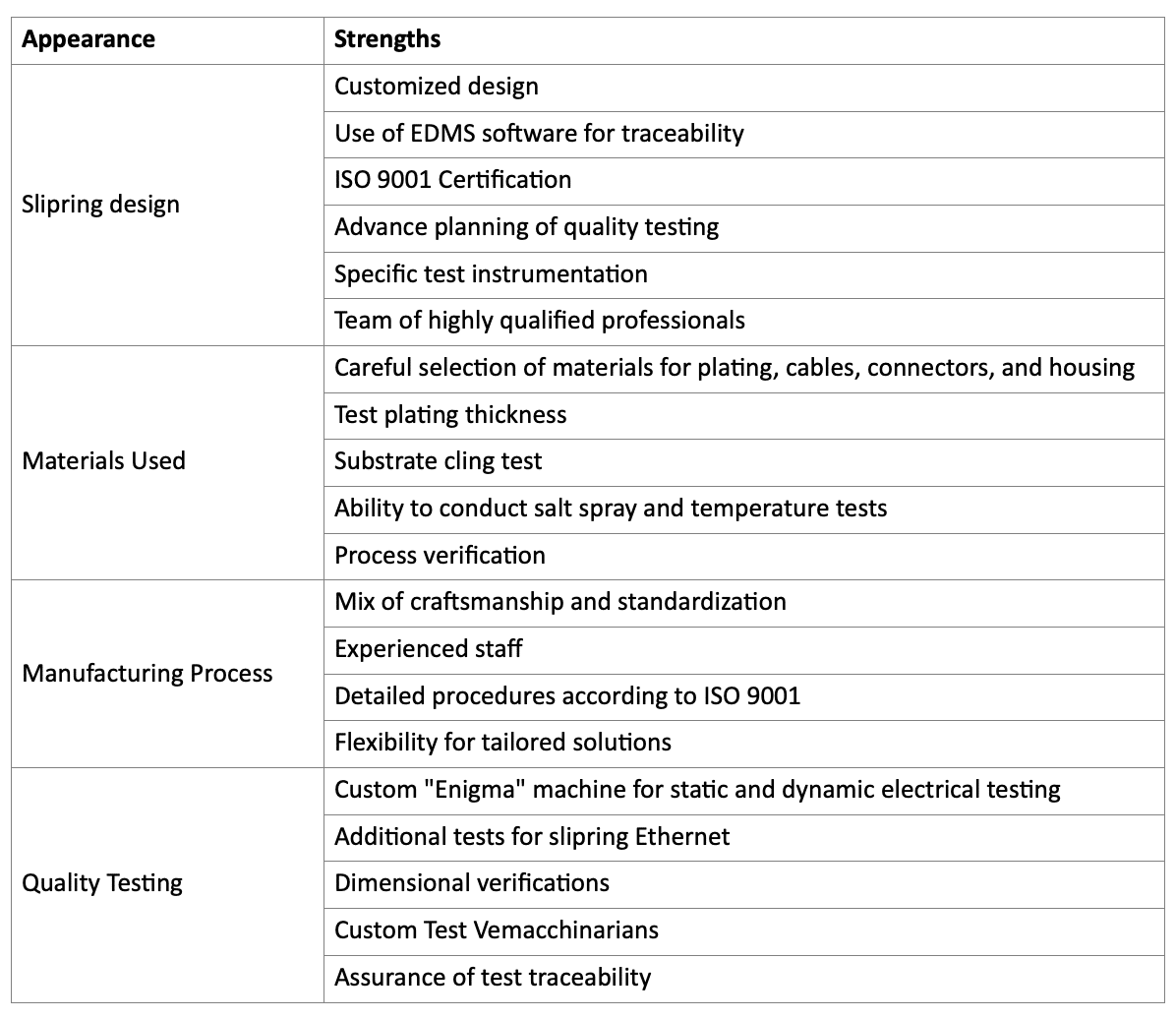
Final Considerations
The design, manufacture and testing of sliprings at Servotecnica are guided by principles of quality, reliability and customization. ISO 9001 certification highlights adherence to international quality standards through all stages of the process.
The use of technologies such as document management software (EDMS) and the custom “Enigma” testing machine, combined with the experience of qualified personnel, supports the goal of maintaining high quality standards. The strict selection and control of materials, together with specific tests, help ensure the reliability of the sliprings supplied.
Flexibility in the manufacturing process enables tailor-made solutions, meeting the complex needs of customers. Servotecnica’s approach aims to provide products capable of meeting operational challenges in various industries, contributing to operational continuity and minimizing downtime.
Commitment to continuous improvement and investment in resources and training represent a determination to maintain a solid position in the industry, ensuring the provision of high-quality and reliable slipring.