Unconsciously, we can tighten a screw by resorting to touch and feel, a faculty we recall for all hobbyist applications. In industrial production, this ability translates […]
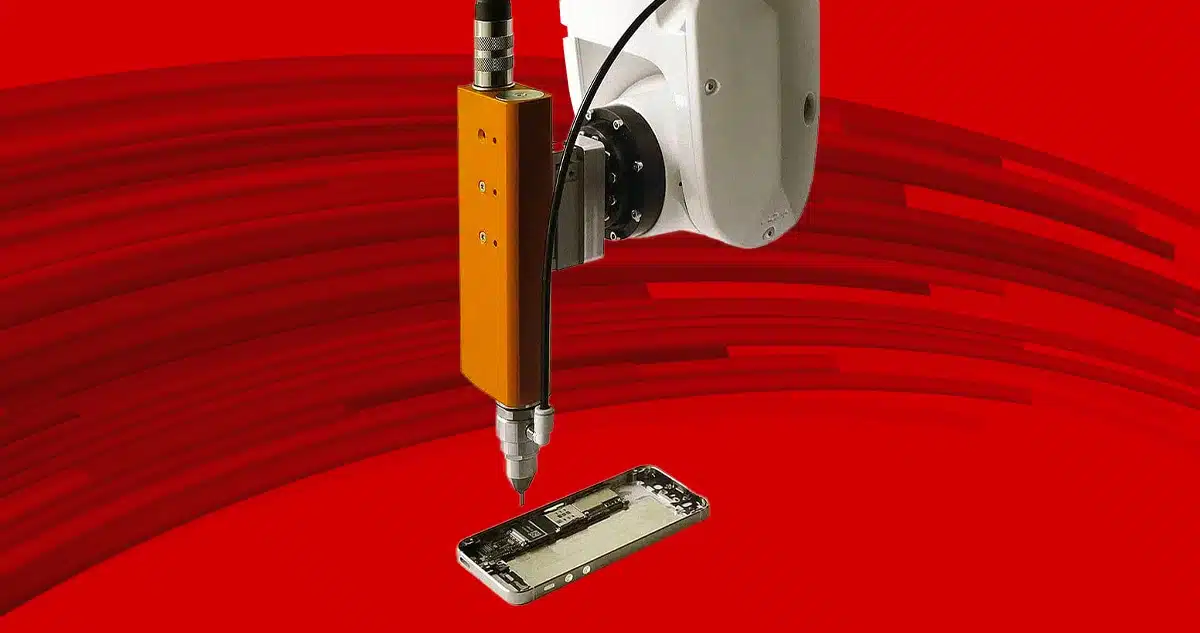
Unconsciously, we can tighten a screw by resorting to touch and feel, a faculty we recall for all hobbyist applications. In industrial production, this ability translates into torque control that ensures secure fastening and durability.
Micro screwdrivers N-Gineric can be used manually or in automated systems. They ensure secure fastening of extremely small screws up to M0.6 used in assembling products such as cell phones, digital watches, and classic wristwatches.
Modifying the chuck covers screw tightenings up to M5.
To ensure the tightening process is reliable, the chucks are equipped with an angle sensor that measures thread position and torque with high precision. Torque is measured based on the deformation of a strain gauge, which deforms proportionally to the torque applied, resulting in a change in resistance. The result is a signal that follows the trend of the applied torque with a very high resolution (24 bits).
Rotor power is supplied by contactless induction via a coil system, 2000 torque measurements are taken every second and transmitted in serial opto-electronically from the rotor to the stator, where they are decoded.
For this type of application, it is important for the motor to have high power in extremely small size and considerable dynamics because rapid torque and speed control is required for each tightening process and during the various tightening stages.
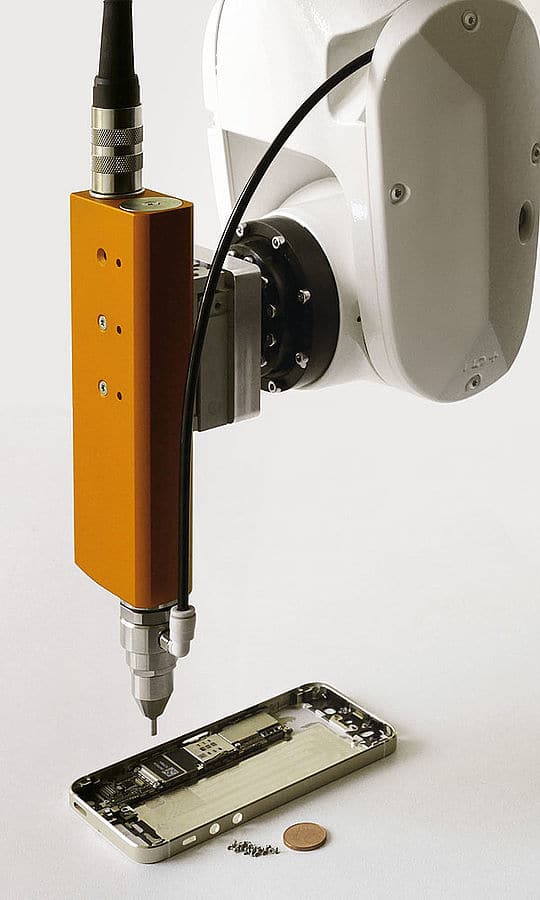
Es: smartphone
No doubt, micromotor, and microrotor play a key role
The brushless micromotor and a planetary gearbox provide the ideal performance. Very short cycles are achieved due to the high acceleration capability, which equates to excellent productivity; the brushless motorization also provides high durability suitable for 24/7 production.
In automotive applications, safety regulations affecting screwdriver systems are particularly stringent (risk class A directive VDI 2862), screwdrivers must be equipped with sensors to measure at least one variable; with these new screwdrivers, both torque and angle of rotation are controlled directly, plus redundancy due to an additional control of a third variable on the current drawn by the motor. All this is to ensure the safety of the system.
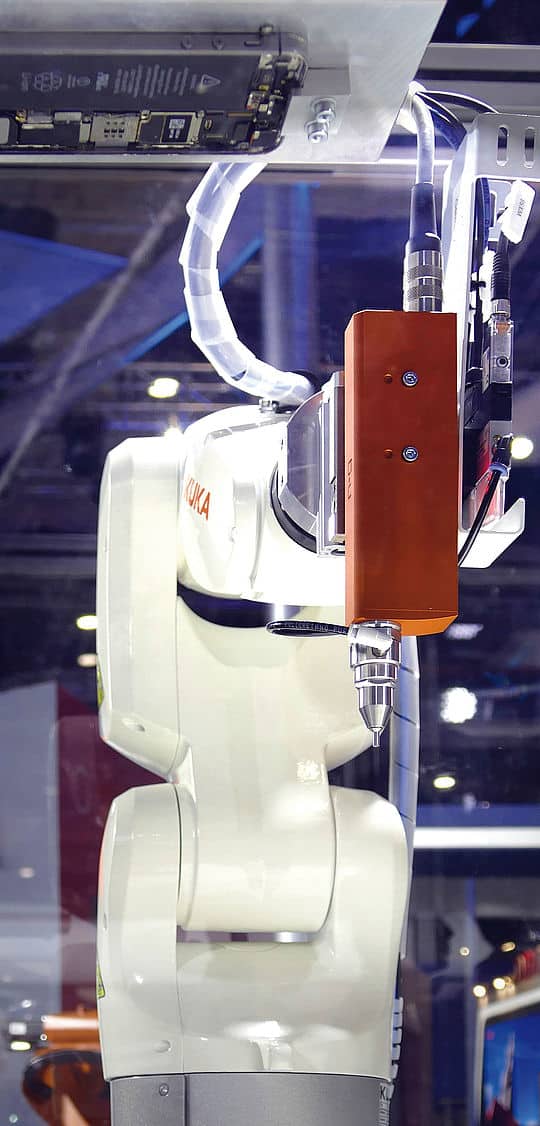
We directly measure torque and angle of rotation.
This type of screwdriver ensures you have chosen the best solution because it protects the automated production process.
The biggest problem in tightening small screws is the small margin between a loose screw or its destruction by excessive torque. This is avoided by employing precision screwdrivers that employ Windows application software to make them simple and intuitive to the operator. Tightening parameters can be set via a real-time display of tightening curves and make process-related documents readily available.
Thanks to the self-adaptive sensors, a system calibration can be performed at the beginning of production.