Linear motion is required for all industrial systems and equipment, from machine tools and conveyor belts to scanning and printing solutions. A conventional motor and a […]

Linear motion is required for all industrial systems and equipment, from machine tools and conveyor belts to scanning and printing solutions. A conventional motor and a suitable mechanical drive component facilitate this straight-line movement. But what if there was a concept that could make linear motion more efficient by using a direct drive? Well, there is. Linear motors have been steadily taking market share across the industrial arena over the past two decades. For those who would like to learn more, read on.
How do linear motors work?
A linear motor provides direct coupling with the load. This direct-drive principle relies upon using a magnetic force to move a coil unit along a track of permanent magnets. To help visualize this configuration, imagine a type of electromagnetic ‘rack and pinion,’ where the pinion is the rotating magnetic field, and the rack is the static, permanent magnets. The attraction and repulsion between the coils and the permanent magnet track create the required motion.
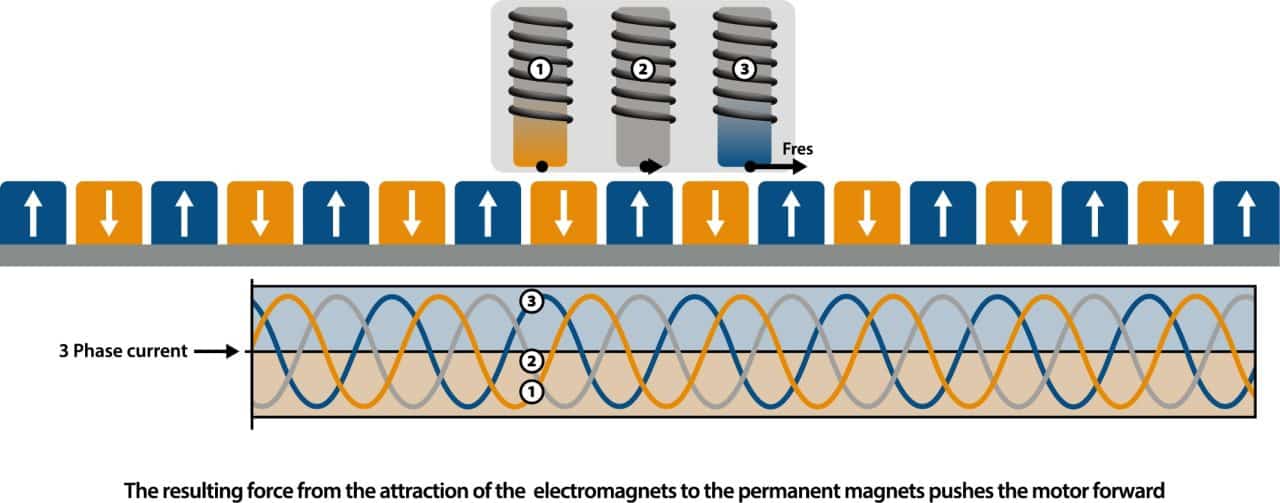
To explain in a little more detail, an alternating three-phase current runs through the coils to generate a rotating (or “translating” in the case of the linear motor) electromagnetic field. This electromagnetic field interacts with the permanent magnet, and the resulting force ultimately converts electrical energy to linear mechanical energy with a high-efficiency level. The speed rate of current change controls the velocity of motion, while the amperage of the current determines the force generated.
Linear motors are not dissimilar to rotary motors in operation, but in a way that sees them opened up and rolled out flat. With permanent magnets, the rotor becomes the stationary part of the linear motor, while the stator (with coil windings) becomes the moving part.
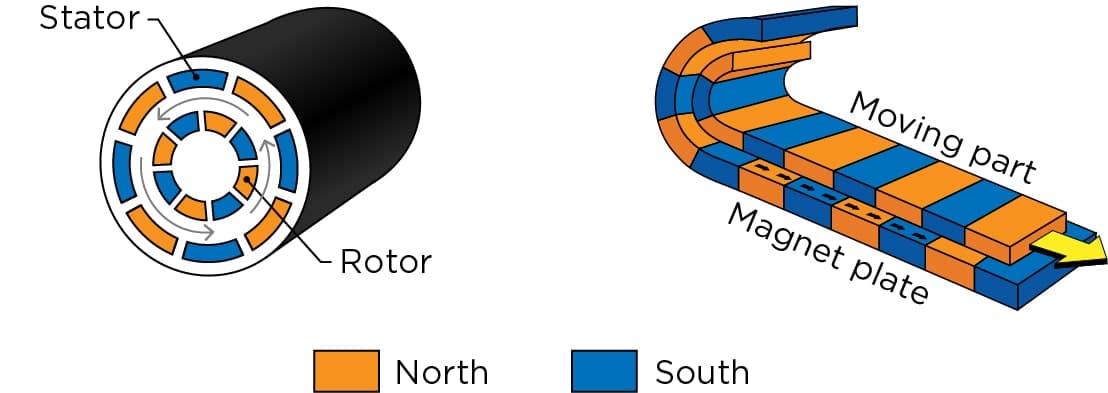
Main benefits
One of the main advantages of linear motors is the elimination of so-called ‘elastic’ transmission components such as gearboxes and couplings, which can lead to issues like backlash and motion/resonance error. As a result, the bandwidth and stiffness of the motion system can be much higher, supporting better repeatability and accuracy.
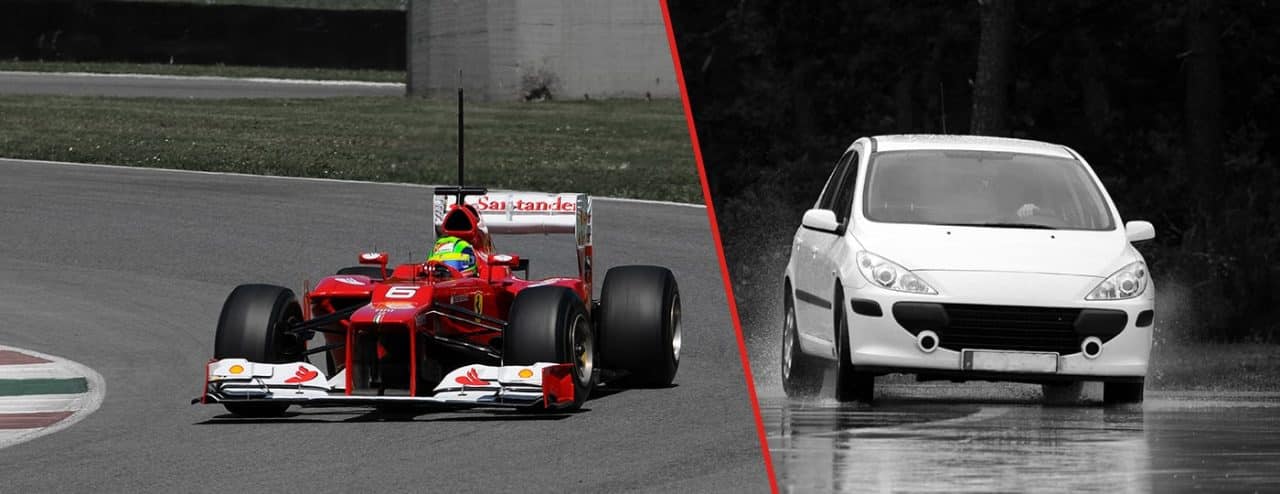
Another significant benefit is removing the need for kinematic drive systems such as ball screws, belts and pulleys, worm gear drives, and rack and pinion systems, which traditional motors need to convert rotary motion into linear motion. Linear motors offer far higher efficiency and positional precision – even at high speeds – while simultaneously achieving very smooth velocity regulation with low ripple.
In contrast to brushed motors, no contact occurs between the moving parts in a direct drive. With no mechanical wear, machine users enjoy exemplary reliability and service life. TCO (total cost of ownership) also reduces compared to traditional solutions.
A further important consideration is space. As the moving part of a linear motor coupled directly to the load, it can save space and simplify machine design, which constitutes a major advantage for system designers and users.
Selection parameters
When choosing a linear motor for a specific application, there are many factors to remember, including the machine’s or system’s dynamic performance requirements. Process parameters such as duty cycle, peak force, and maximum speed often come to the fore.
Two principal types of linear motors are available. Any application with a light payload that necessitates extremely accurate movements or high acceleration will usually take advantage of an ironless linear motor. However, iron-core linear motors produce greater continuous force for applications requiring a high-duty cycle.
Iron-core linear motors
The design of iron-core linear motors sees the mounting of coil windings within an iron lamination stack to amplify the amount of electromagnetic flux produced. This type of linear motor offers extremely high continuous force and good heat dissipation for its size, making it ideal for applications involving large payloads. Examples include machine tools, such as milling, turning, pressing, molding, laser cutting operations, and textile production machinery.
One drawback many engineers associate with iron-core motors is cogging, a parasitic force due to the generation (by permanent magnets) of a fluctuating attraction force to magnetic materials like iron. In short, the iron core has ‘preferred’ positions in relation to the magnets, so the motor must vary its thrust force to overcome these locations, resulting in an unsmooth ‘cogging’ motion.
Modern solutions, however, with their optimized iron-core design, restrict this historical problem to delivering low-cogging performance. By way of example, some linear motors feature magnets that are not orthogonal to the direction of motion but are instead set with a small angle of skew, which helps smooth the movement sufficiently to address a large number of common industrial applications.
Ironless linear motors
Ironless linear motors have no attraction force or cogging between the coil unit and the magnet track. As a result, ironless variants offer no ripple force, high precision, a constant linear force, and high velocity and acceleration. Furthermore, ironless linear motors work in 95% of cases by moving the lighter coil unit, which helps achieve higher dynamic movement and constant speed. The extremely thin shape of ironless variants is also beneficial as it provides machine builders with flexible mounting options.
Potential applications for this type of linear motor are wide and varied; essentially, any machine or system moving a small mass at high speed and high precision. Examples include semiconductor manufacturing solutions, testing machines, microscope or inspection stages, and automated equipment for medical or life science laboratories.
Conclusion
There are many reasons why the adoption of linear motors has soared in recent years. Not only does this type of motor deliver high force over a wide spectrum of speeds, but its availability in an extensive size range makes it easily adaptable to most applications. Ultimately, selecting a linear motor will provide an efficient and effective gearless assembly to machine builders and users.
For advice on linear motor selection in relation to specific applications, always engage with a specialist to provide complete system-integrated solutions. This factor is important as machine builders must consider not just the linear motor but the linear encoder (for feedback) and servo drive, which should be at the same high level of specification to ensure accurate, smooth motion.