Mobile grippers have enormous potential in manufacturing processes as collaborative assistants for commissioning and pre-assembling components or for automatic replenishment of automated machines. We focus on […]

Mobile grippers have enormous potential in manufacturing processes as collaborative assistants for commissioning and pre-assembling components or for automatic replenishment of automated machines. We focus on key challenges encountered on the experimental platform (christened omniROB) at the Institute of Robotics at Johannes Kepler University in Linz, Austria:
- Realization of a robot that can offer high maneuverability and agility
- Cognition of its surroundings
- Safe and collision-free navigation of the robot base and arms
Traditional platforms (car platforms) are mostly built on a four-wheel base with two swivel wheels. While they are very reliable, they cannot move sideways or rotate on themselves. However, these operations are essential when considering the need to move in environments with limited maneuvering space as manufacturing areas normally are. Our mobile platform overcomes these limitations by using special “Mecanum” wheels. These allow the robot to move instantly in all directions. Robots operating on industrial floors must be able to relate to dynamic environments. By “dynamic,” we mean that, on the one hand, we have to consider that some objects (such as forklifts, people, etc.) operate near the robot, so the navigation scheme has to deal with constantly changing situations or even predict the behavior of its surroundings; the platform has been equipped with ultrasonic distance sensors capable of sensing the surroundings at 360° to perceive neighboring objects. On the other hand, observing the surrounding environment is used to locate the robot’s position. Thus, if the environment changes (such as when a pallet is moved), the robot must recognize it and reconstruct the map used for its own location. Ultrasonic sensors are neither safe nor accurate enough to determine the correct location. That is why we added an additional LIDAR (light detection and ranging) sensor that allows the platform to reconstruct its surroundings in real-time. The platform, made of particularly lightweight materials, has an arm with seven rotary joints and a gripper. It is already being used to collect materials and will be used for pre-assembly functions in the future. Since the arm is not placed in an enclosed and confined environment, it is necessary to probe the environment for possible collisions with objects or people before starting any movement to define a collision-free trajectory.
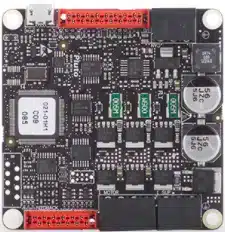
The arm is controlled by PLUTO series servo drives by INGENIA employed in interpolated position mode. True Host computer communication, which is responsible for calculating the desired path, is via the CANopen protocol. More sophisticated control schemes, including force control, will be investigated to compensate for even small positioning errors that are particularly bad for operations requiring higher accuracy.
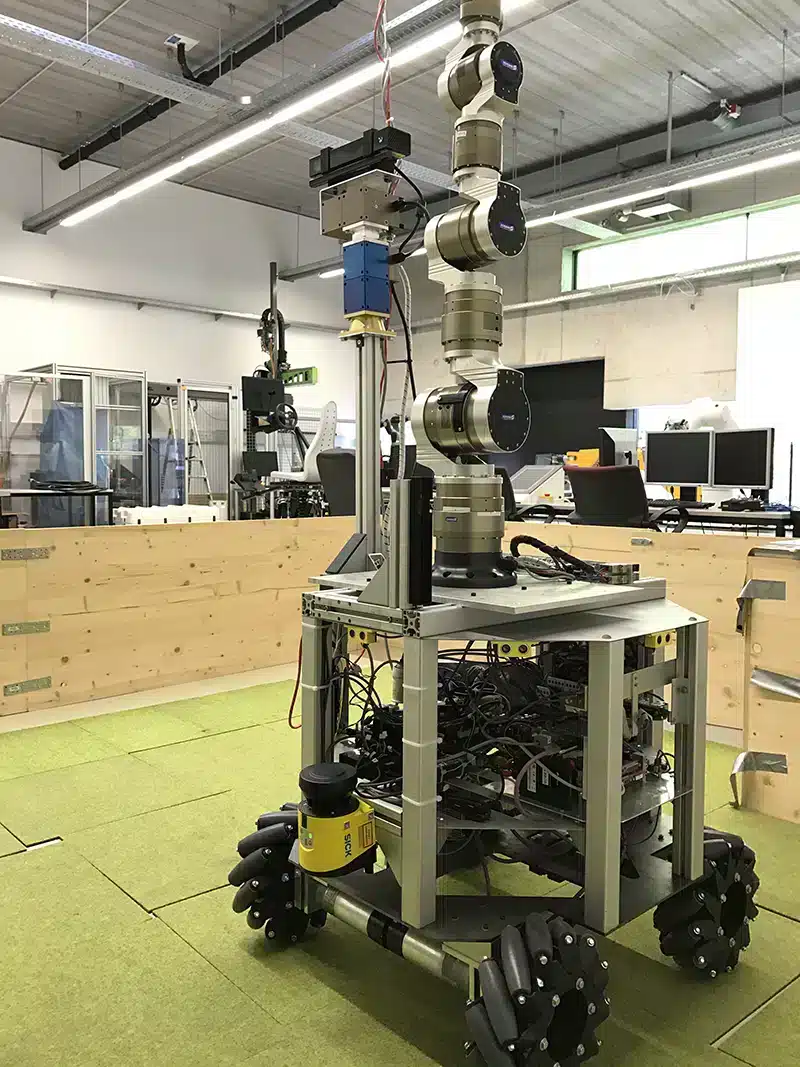
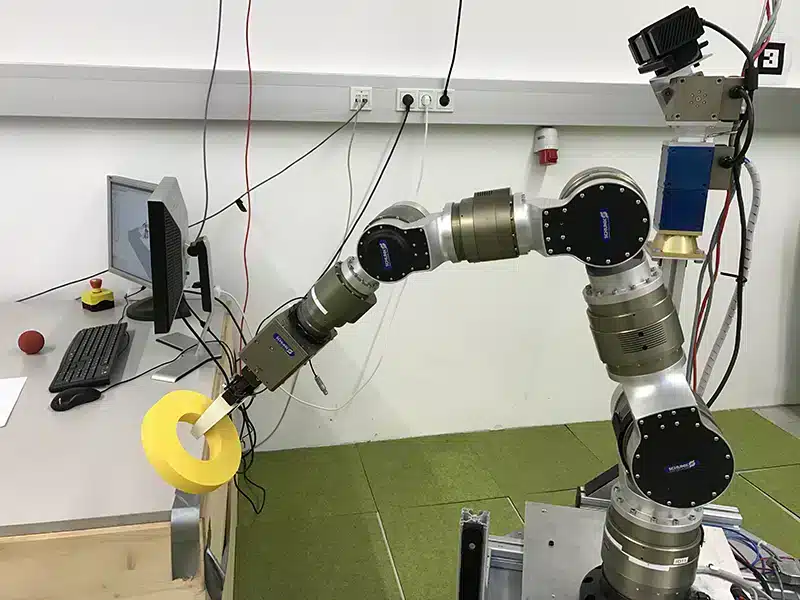
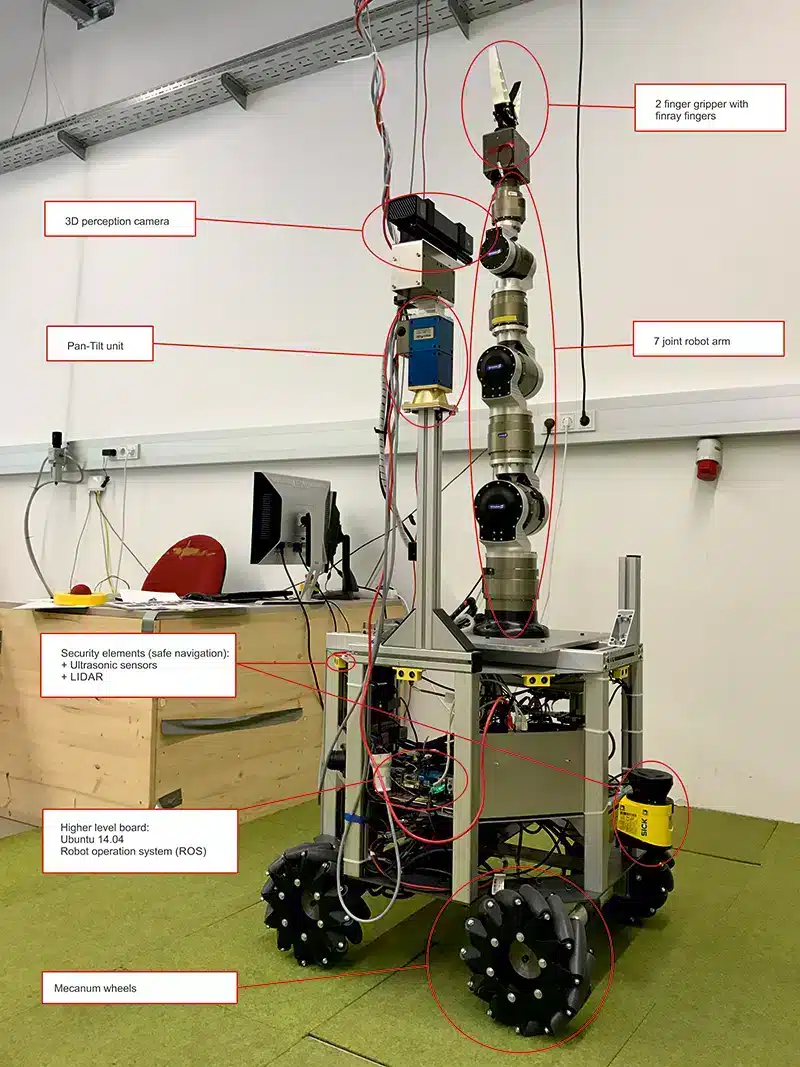
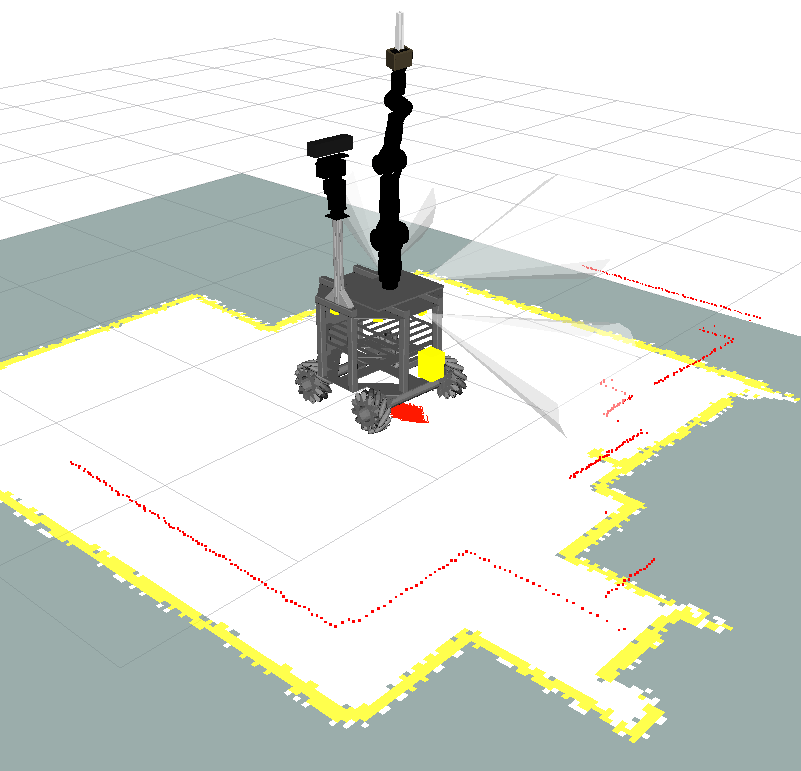
Digital drive PLUTO by INGENIA for omnidirectional COLLABORATIVE Robot